Sand cast aluminum parts series
-
Low pressure cast aluminum series
-
Sand cast aluminum parts series
-
Die cast aluminum parts series
-
Mechanical processing series
-
Sand casting aluminum series
-
Gravity Casting Series
-
Sand cast aluminum parts series
-
Die cast aluminum parts series
-
Electromagnetic gas emergency shut-off valve
-
Domestic gas emergency shut-off valve gas leakage

Hot Product
News
2024-05-12
2024-05-12
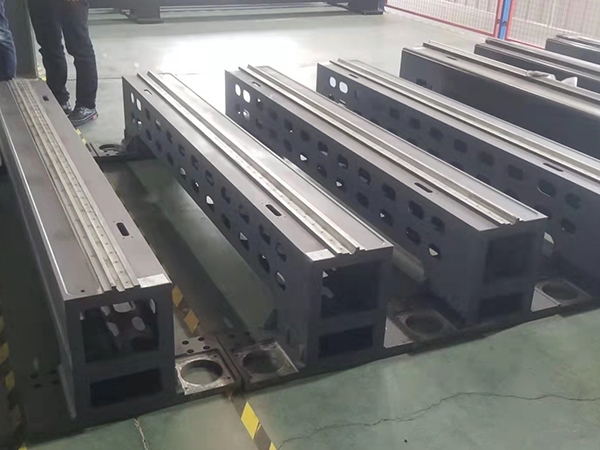
Sand cast aluminum parts manufacturer - Botou Quanle Metal Products Co., Ltd
The heat treatment process of cast aluminum pipe fittings can be divided into the following four categories:
1. Annealing treatment heats sand cast aluminum castings to a higher temperature, generally around 300 ℃. After holding for a certain period of time, the process of cooling them to room temperature in the furnace is called annealing. During the annealing process, the solution decomposes and the phase particles aggregate, which can stabilize the internal stress of the casting, reduce deformation, and increase the plasticity of the casting.
2. Solid solution treatment heats the casting to a temperature as high as possible, close to the melting point of eutectic, maintains it at that temperature for a sufficient amount of time, and then cools it to dissolve the components. This high-temperature state is fixed and stored at room temperature, and this process is called solid solution treatment. Solid solution treatment can improve the strength and plasticity of castings, as well as the properties of alloys. The effectiveness of solid solution treatment mainly depends on the following three factors:
1. Insulation time. The insulation time is determined by the dissolution rate of elements, which depends on the type, composition, structure, casting method, and shape and wall thickness of the alloy. The insulation time of cast aluminum alloy is much longer than that of deformed aluminum alloy, usually determined by experiments. Generally, sand mold castings are 20% -25% longer than metal mold castings of the same type.
2. Cooling speed. The higher the cooling rate given to the casting during quenching, the higher the supersaturation of the solid solution preserved from the high-temperature state, thereby achieving high mechanical properties of the casting. However, at the same time, the greater the internal stress formed, the greater the possibility of deformation of the casting. The cooling rate can be changed by selecting cooling media with different heat capacities, thermal conductivity, latent heat of evaporation, and viscosity. In order to reduce internal stress, castings can be cooled in hot media (boiling water, hot oil, or molten salt).
3. Solid solution treatment temperature. The higher the temperature, the faster the dissolution rate of elements, and the better the effect. The upper limit of the general heating temperature is lower than the initial overburning temperature of the alloy, while the lower limit of the heating temperature should allow as many components as possible to dissolve into the solid solution. In order to achieve a solid solution effect without the inconvenience of alloy overburning, sometimes a graded heating method is used, which is to maintain insulation at a low melting point eutectic temperature, so that after the diffusion and dissolution of the components, the low melting point eutectic does not exist, and then rise to a higher temperature for insulation and quenching. During solid solution treatment, attention should also be paid to the heating rate not being too fast to avoid deformation of aluminum alloy castings and the melting of low melting point structures that accumulate locally, resulting in overburning. The heat transfer time of solid solution heat treatment should be as short as possible, generally not more than 15 seconds, to avoid the diffusion and precipitation of alloy elements and reduce the performance of the alloy.
3. In order to ensure the uniformity of temperature inside the furnace meets the quenching process requirements of aluminum alloy workpieces, a centrifugal fan is also installed at the top of the furnace body. The centrifugal fan can circulate the hot air flow under the action of the furnace guide system, which is made of heat-resistant stainless steel plate. In order to prevent deformation inside the furnace, the guide plates are all installed in a suspended manner, with stable structural performance and long-term operation of the equipment without maintenance.
4. The lifting of the material rack is completed by a lifting hoist set outside the furnace, which is equipped with a dual speed drive for loading. When the furnace door is opened, the hoist automatically descends and quenches the fully loaded workpiece material rack in water. When the material rack is ready to enter the furnace again, the hoist lifts the material rack at a slow speed to prevent the inertia of the workpiece movement, operate smoothly, and not damage the sealing device and insulation material of the furnace mouth.